Cardboard Shredders
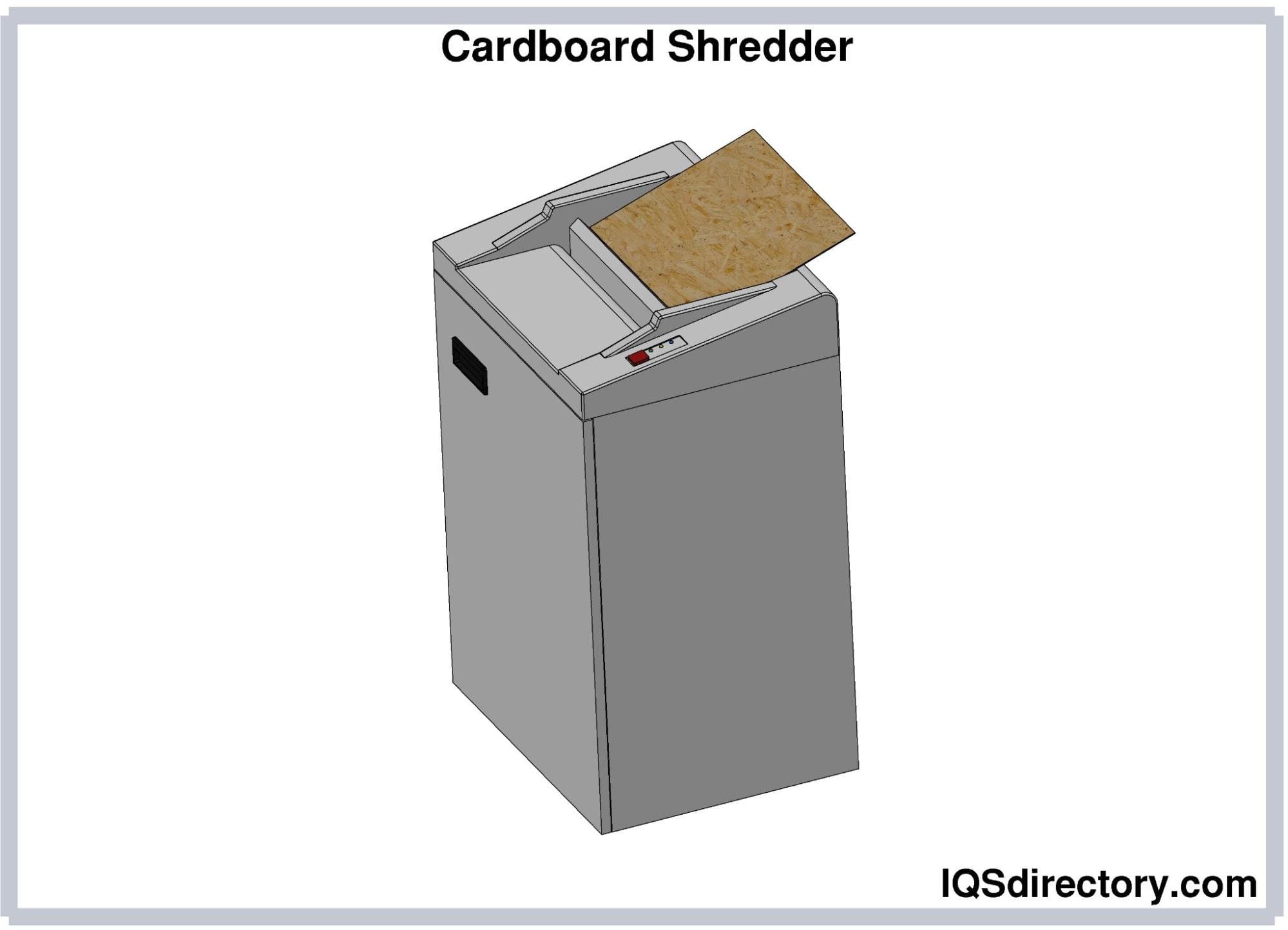
A cardboard shredder is a machine designed to turn cardboard boxes and sheets into small shards or strips. Specialty cardboard shredders are configured to convert cardboard into flexible perforated material for packaging...
Please fill out the following form to submit a Request for Quote to any of the following companies listed on
This article will take an in-depth look at shredding machines.
The article will bring more detail on topics such as:
This chapter will explore the concept of shredding machines, including their design, construction, and operational mechanisms.
A shredding machine is a device designed to cut or shred materials into smaller pieces. Although many online sources refer to shredding machines primarily as tools for shredding documents to protect privacy and prevent identity theft, these machines come in various types tailored to different materials and applications.
Shredding machines are engineered to handle a variety of materials for different recycling applications. These include plastic recycling, scrap metal processing, e-waste management, wood recycling, and tire shredding or recycling.
The shredding operation produces raw materials to be re-introduced into manufacturing, as well as complete products like landscape mulch. Many terminologies are utilized to describe size reduction machines, including grinders, granulators, chippers, and hammer mills. Overall, their main purpose is to reduce the size of a given material.
The design and construction of shredding machines encompass the following elements:
Shredding machines are composed of several key components: feed shafts (for industrial models), a feed zone where materials are introduced, crushing gears or slicing blades, a motor that powers the blades, and a chute (for industrial use) that directs the shredded materials onto a conveyor for further processing or into a container for disposal.
Most shredding machines are equipped with screens to capture material that is still too large after the initial shredding. To ensure thorough processing, this oversized material is fed back through the machine repeatedly until it reaches the desired size.
Designing a shredding machine involves considering several factors, such as the type of material to be shredded, the volume of material, the operating environment (e.g., farm, office, outdoor, indoor), the space allocated for the machine, the frequency of use, and the client's budget.
The size and shape of hooks on shredding cutters vary depending on the material they need to handle. Generally, larger hooks can grab more material, which can enhance production rates. However, it is crucial to ensure that the hooks do not exceed the shredding machine’s capacity to process material at one time, as this can lead to frequent jams and reduced production efficiency. Shredding blades are often made from tool steel and carburizing steel, though other materials such as molybdenum, chromium, and manganese low alloy steels are used for specific applications.
The design of shafts primarily involves calculating the appropriate diameter to ensure adequate rigidity and strength while the shaft transmits power under various loading and operating conditions.
The material selected for the shaft should possess the following characteristics:
Carbon steel is primarily utilized for the shaft, but when high strength is needed, alloy steel like nickel-chromium, nickel, or chrome-vanadium is used.
Electric Drives – This system powers the rotation of the blades and varies in size depending on the shredding machine type. Small shredders, such as paper shredders, may use DC motors, while metal shredders often employ three-phase AC induction motors. Generally, electric shredding machines are more compact, easier to operate and maintain, and more energy-efficient compared to hydraulic shredders. They are also cost-effective and suitably powerful for processing a wide range of materials.
Hydraulic Drives – Hydraulic drives serve the same purpose as electric drives but are often preferred for heavy-duty applications, such as tire shredding. They are particularly effective in handling materials that experience frequent overloading from batch feeding. Consequently, hydraulic drives are typically found in industrial shredders. They also offer superior protection against shock loads from unshreddable materials.
Scenarios where a hydraulic drive system is suitable include:
The design of a shredding machine can vary significantly based on its application, ranging from compact, hand-fed models suitable for office or home use to large-scale machines capable of processing thousands of kilograms per hour in commercial shredding facilities.
There are three primary methods of shredding described below:
Shearing involves cutting materials with blades, similar to how scissors work. The efficiency of shearing depends on the sharpness of the cutting edges and the precise spacing between them. Technologies like ACLS and annealed alloys help maintain this sharpness and tolerance, ensuring clean cuts even over prolonged use.
Tearing involves applying force to pull materials apart. Materials such as fabric, soft metals, tires, and plastics are more prone to tearing. Machines designed for tearing are effective for processing mixed waste materials where uniform particle size is less critical.
Some materials, like hard plastics, glass, and certain metals, are brittle and tend to break or shatter in shredding machines. If the cutters are not adequately sharp or if they are loose, the material may release explosive energy and potentially propel shards, so eye protection is essential.
All three actions—tearing, shearing, and fracturing—can be employed in shredding machines. However, with sharp cutters and precise tolerances, shearing is usually the most efficient shredding action.
Different materials are best processed with specific shredder types and settings. The physical properties of each material affect how it responds to shredding.
Ductile Material – Ductile materials resist fracturing and are prone to tearing into long strips. Shearing is ideal for these materials to ensure a smaller particle size. Examples include paper, cloth, soft plastics, rubber, soft metals, and cardboard.
Friable Materials – These materials fracture easily, the opposite of ductile materials, and are broken into shards. Examples include glass, stone, cast metals, wood, and hard plastics. Shredded friable materials generally come out as small pieces rather than long strips.
Several factors should be considered when selecting a shredding machine:
Different shredders are optimized for specific materials. For instance, a tree branch is typically processed with a high-speed chipper, while plastics are often first shredded before being granulated. Car shredding is usually performed with a hammer mill. A twin-shaft shredder might be best for diverse waste products, minimizing dust and noise.
Determining the required output size helps in selecting the appropriate equipment. Some operations need items to be separated, while others might require further shredding or grinding. A single-pass shredder may be more cost-effective, but highly reduced sizes may require additional compaction machinery.
Selecting a shredder with the right capacity is crucial for successful operation. Capacity is typically measured in kilograms per hour and is influenced by physical dimensions, weight, and the volume of material. Ensure the machine has a slightly higher capacity than required to avoid excessive wear or power consumption.
Verify the capacity rating before purchasing and allow for some extra capacity. Using a shredder at its maximum capacity can lead to reduced lifespan, while an oversized machine may result in excessive power use and occupy unnecessary floor space.
Two common feed types are: automatic and manual. Manual shredders often include a hopper for hand-feeding or using a forklift to load materials. Automatic feeders or conveyors enhance performance by providing a continuous supply of materials to the shredder.
When choosing a shredding machine, consider factors like safety, portability, and noise. It is essential to choose an appropriate location for the shredder, as moving heavy machinery can be challenging. Additionally, dust and airborne debris can pose environmental hazards, and noise levels vary between machines.
Shredders endure significant stress, so regular maintenance is necessary to ensure efficient operation. Cutters, hammers, or blades will eventually wear out and need adjustment, sharpening, or replacement. Consider the ease of obtaining replacement parts and the accessibility for maintenance when choosing a manufacturer and placement of the equipment.
The different types of shredding machines are:
A cardboard shredding machine is a commercial or industrial recycling device designed to convert cardboard waste into useful packaging materials. These machines can produce various forms of packaging material, including cushioning netting, chips, flat netting, or strips.
Operating similarly to a paper shredder, a cardboard shredding machine processes discarded cardboard boxes to create eco-friendly and high-quality cardboard void fill materials, such as strips, chips, or netting. The machines are user-friendly, easy to operate, and designed with safety in mind. To use the machine, simply turn it on with a switch, feed a piece of cardboard through the front opening, and collect the shredded material from the back of the shredder.
A cardboard shredding machine efficiently transforms cardboard waste into reusable packaging materials. This process not only helps reduce waste disposal costs but also eliminates the need for purchasing new packing materials. The machine produces void fill materials in various sizes and shapes to safeguard goods during transportation, all while repurposing cardboard waste in an environmentally friendly manner.
A paper shredding machine is electronic equipment used to shred (usually sensitive or confidential) paper documents into indecipherable particles. The shredding machine shreds documents using a set of spinning cutting blades spun by an electric motor.
The size of the output pieces varies based on the type of paper shredding machine. Shredders are typically classified into strip-cut, cross-cut, and micro-cut categories. Depending on the model, a shredding machine can produce paper fragments as small as confetti or long strips. The output of paper shredding machines adheres to the security levels established by DIN 66399.
Paper shredding machines do not all produce the same cut size. In other words, different machines create particles of varying sizes. To differentiate between them, paper shredding machines are categorized into three types:
A strip cut shredding machine (also known as ribbon cut, straight cut, or spaghetti cut) is designed for shredding non-confidential documents. It slices paper into long, narrow strips that remain relatively readable.
This type of shredder offers the benefit of being easy and quick to operate due to its straightforward cutting mechanism.
However, a strip cut shredding machine provides less data protection compared to cross-cut or micro-cut shredders. The characteristics of strip cutting include:
A cross cut shredding machine (also known as confetti cut or diamond cut) is designed for shredding confidential documents. It cuts paper diagonally from two corners into small pieces that are nearly unreadable. Cross cut shredders with P-4 or P-3 security levels are well-suited for disposing of sensitive personal information or private documents in a workplace setting. Its characteristics include:
A micro cut (also known as particle cut or security cut) shredding machine is a high-security paper shredder designed for handling highly confidential documents. It cuts paper diagonally from two corners into small, square-shaped pieces that are nearly impossible to read. Its characteristics include:
A plastic shredding machine is designed to break down large plastic items into smaller pieces for further processing. Unlike plastic granulators, which are suited for smaller, more uniform plastic waste, shredding machines handle larger plastic products such as car bumpers, drums, pipes, and other sizable items that cannot be processed by granulators.
During operation, large plastic items are fed into the shredding machines. The blades, operating at slower speeds compared to granulators, break the plastic into smaller chunks. These particles are then collected, cleaned, and processed in recycling facilities before being granulated and supplied to manufacturers.
In addition to breaking down plastics for use as raw materials in products like storage containers, packaging bags, toys, and consumer electronics, plastic shredding machines offer several advantages. They are utilized across various sectors, including the plastic industry, catering industry, laboratories, manufacturing units, pharmaceutical companies, biomedical waste management plants, food processing facilities, nursing homes, cardboard manufacturing units, healthcare facilities, and supermarkets.
Hard drives often contain sensitive data, ranging from financial records and social security numbers to critical plans. Hard drive shredding is a commonly used method for physically destroying hard drives. While a hard drive shredder crushes the drive to make data retrieval more difficult, it does not completely eliminate the possibility of recovery. Modern technology means that even shredded particles, which can be as small as 2 mm, may still hold up to 600,000 data pages—smaller than a grain of rice!
A common misconception is that shredding media makes the data completely unrecoverable. However, physically destroying or shredding the media does not erase data from the disk platters, as data is stored magnetically. Tools and applications available online can recover data from larger particles of a shredded drive. Even smaller particles can be analyzed using magnetic force microscopes to retrieve information.
Tire shredders are shredding machines that are capable of reducing tires into a constant particle size. This type of shredder can also be utilized for a wide range of materials such as aluminum, plastics, paper, and cables. The tire shredding is capable of reducing tires and hence making recycling of tires easier. The end result, the tire waste, may often be sold.
A chipper shredder, also known as a wood chipper, processes twigs, branches, and leaves into compost and mulch, contributing to the maintenance of attractive landscapes. Chipper shredders range from light-duty electric models to heavy-duty gasoline-powered machines capable of handling branches several inches in diameter.
A chipper shredder is equipped with a chute where branches are fed for chipping. A rotating blade or multiple blades break the branches into wood chips. For smaller debris like grass and leaves, the machine uses a different shredding mechanism, which typically involves a set of hinged blades, also known as hammers or flails. Larger shredding machines can handle small twigs as well. After processing, the shredded or chipped material is expelled into a collection bag or directly onto the ground.
The shredder's hopper and chipper chute are designed to keep the user safely away from the chipping and shredding mechanisms. Some models include a tamper or paddle to assist in feeding debris, ensuring that hands remain clear of the operating parts.
Metal shredders are machines designed to process a variety of scrap metal. They are commonly used in metal recycling facilities and scrapyards to break down metal waste into uniform sizes and shapes for easier disassembly and subsequent processing.
Metal shredders come in various sizes, ranging from smaller units that can handle items like coins and tin cans to large-scale models capable of operating at 10,000 horsepower and processing up to 4,000 tons of metal per day. These larger machines are used to shred vehicles as part of the end-of-life car recycling process, large drums, and virtually all types of scrap metal.
This chapter will cover the applications, benefits, and standards associated with shredding machines.
Industrial shredding machines are used across a range of applications to process various materials. These include foods, pharmaceuticals, pallets, rubber, steel, furniture, plastic drums, construction debris, containers, tires, corrugated boxes, labels, packaging, and other large items. Additionally, shredding machines are employed to reduce documents, x-rays, hard disk drives, and other electronic devices to protect personal and corporate privacy.
In municipal settings, shredding machines are commonly used at recycling centers and wastewater treatment plants. Smaller shredders with numerous cutting teeth are utilized for thorough reduction. The recycling industry benefits from shredding machines that process tires to recover rubber, which is then used in products like hot melt asphalt, playground surfaces, basketball courts, and footwear.
Recycled rubber also finds use in civil engineering for backfilling, road insulation, and as "Tire Derived Fuel." Shredded scrap wood is recycled into various wood products such as particleboard and paper. Plastic bottles are shredded and recycled into polyethylene terephthalate (PET) for producing new bottles. By shredding these materials, environmental waste is minimized, corporate profitability is enhanced, and carbon emissions are reduced.
Shredding machines are integral to numerous applications, including recycling, manufacturing, solid waste reduction, wastewater treatment, security, oil and gas production, and bio-solids management. Beyond simple size reduction, shredding machines offer many advantages such as producing raw materials or fuel, protecting sensitive information by destroying confidential documents, recycling waste, and ensuring the smooth operation of other processes and equipment. Shredders are utilized by corporations, municipalities, and government agencies alike.
Enhance Security – A primary benefit of having a high-quality shredding machine is the improvement in data security for a business. It is essential for modern enterprises to ensure that sensitive information remains inaccessible to unauthorized individuals. Effective shredding machines help protect confidential data from being exposed to unintended parties, fulfilling both competitive and regulatory requirements.
Reduce Waste Volume – Shredding documents and other media reduces the volume of waste produced by a business. This reduction in waste size streamlines waste management processes and can lower costs, particularly when waste disposal fees are based on volume.
Cut Costs – Purchasing a personal shredder can lead to significant cost savings compared to outsourcing shredding services. Quality shredding machines are now more affordable and accessible for businesses of all sizes. The long-term savings of having an in-house shredder versus paying for external shredding services can be substantial. Additionally, having a shredder on-site enhances security by eliminating the need to send sensitive information off-site for destruction.
Boost Efficiency – Owning a personal shredder can greatly improve operational efficiency. With an on-site shredder, there’s no need to wait for third-party shredding services or deal with the logistics of organizing and storing documents before destruction. Sensitive information can be shredded immediately, reducing delays and improving workflow.
These are some of the fundamental advantages that a shredding machine offers a business. However, the benefits can vary depending on the type and scale of the shredding equipment chosen.
Here are some potential drawbacks of using machine shredders:
To ensure the safety of operators, employers should train their staff on proper shredding practices, including safe loading and unloading procedures. OSHA provides comprehensive guidelines and standards for workplace safety. As a leading safety regulatory body, OSHA is highly recognized for its work safety regulations. It's crucial for customers to verify that their shredding machines are OSHA certified to ensure compliance.
Additionally, many industries, including metal recycling, adhere to OSHA regulations. Therefore, it is important to be aware of and follow the specific safety and compliance standards applicable to the industry and the shredding equipment used.
Shredding machines can be categorized into industrial and consumer types based on their intended use. Typically, paper shredding machines are considered consumer shredders, as they are primarily used by individuals or small businesses.
Industrial shredders, on the other hand, are robust and designed for high-volume applications. They handle a wide range of materials, including plastics, electronic waste, wood, and paper. These shredders feature various cutting mechanisms, such as horizontal and vertical shaft designs, as well as single, dual, triple, and quad-shaft cutting systems.
There are various factors to consider before choosing a suitable shredding machine. Collecting all the important information to compare against the shredding machine specifications will aid in shortening the process of comparing the equipment to the requirements. For recycling, the necessary permits must be at hand. Seeking knowledge and advice from a trustworthy company is a great start, and asking for a demonstration using a sample will approve the shredding machine’s effectiveness. Visiting a manufacturer’s website to check the company’s background and going through some case studies to learn how other companies have used shredding machines to solve operating difficulties is also a good start. The last step of the equation is figuring out the budget. Keep in mind that some machines, though initially less expensive, can be inferior in quality and in actuality are costlier in the long term to use and maintain.
A cardboard shredder is a machine designed to turn cardboard boxes and sheets into small shards or strips. Specialty cardboard shredders are configured to convert cardboard into flexible perforated material for packaging...
An industrial shredder is a piece of heavy duty equipment designed to shred dense and light materials to prepare them for recycling or for the destruction of unusable products. They are an environmentally sound device that...
Scrap metal must be processed to be effectively recycled and ready for reuse. Metal shredders are machines used to process a variety of metal scraps. Metal shredders are frequently used to reduce metal debris to...
Tire shredders are a type of recycling equipment used to reduce the volume of tires to scrap using high torque shredding systems. The various types of tire shredders are capable of handling large loads of...
A baler is a piece of equipment used to compress solid industrial waste or recyclable materials (e.g., paper, plastic, foam, cans, etc.) to achieve better material handling and storage. Eliminating empty space between individual items of these bulk products is a great way to save costs attributed to storage and transport...
A bowl feeder is a mechanism for supplying small parts and components to a production line or for sorting bulk items for rapid use. A self contained bowl feeder system has a bowl that sets on a spring loaded base that moves vertically...
A cardboard baler is a mechanism that uses a metal plate driven by a hydraulic ram to apply tremendous pressure and force to crush, compact, and compress pieces of cardboard into tightly formed and easy to transport cubes and...
A Trash compactor is a machine or device designed to compress, reduce, and compact a variety of materials through hydraulic, mechanical, or pneumatic force. The initial steps in the compacting process are the collection of the material to be compacted...
Vibratory conveyors are material-handling equipment used to transport fine to coarse-grained bulk materials. These vibratory conveyors are strong conveying equipment utilized for bulk commodities with fine to coarse graininess...
Vibratory feeders are short conveyors used to transport bulk materials utilizing a controlled vibratory force system and gravity. The vibrations impart a combination of horizontal and vertical acceleration through tossing, hopping, or sliding-type of action to the materials being handled...
A vibratory screening is a process that separates bulk solid materials from solids and slurries using inertial vibration that causes various sizes of particles to pass through openings in a screen or...
Modern balers are descendants of hay presses, invented in the mid-nineteenth century, that made it easier to gather and stack hay. The earliest hay presses were stationary units built into a barn and extending two to three stories into the hayloft...